
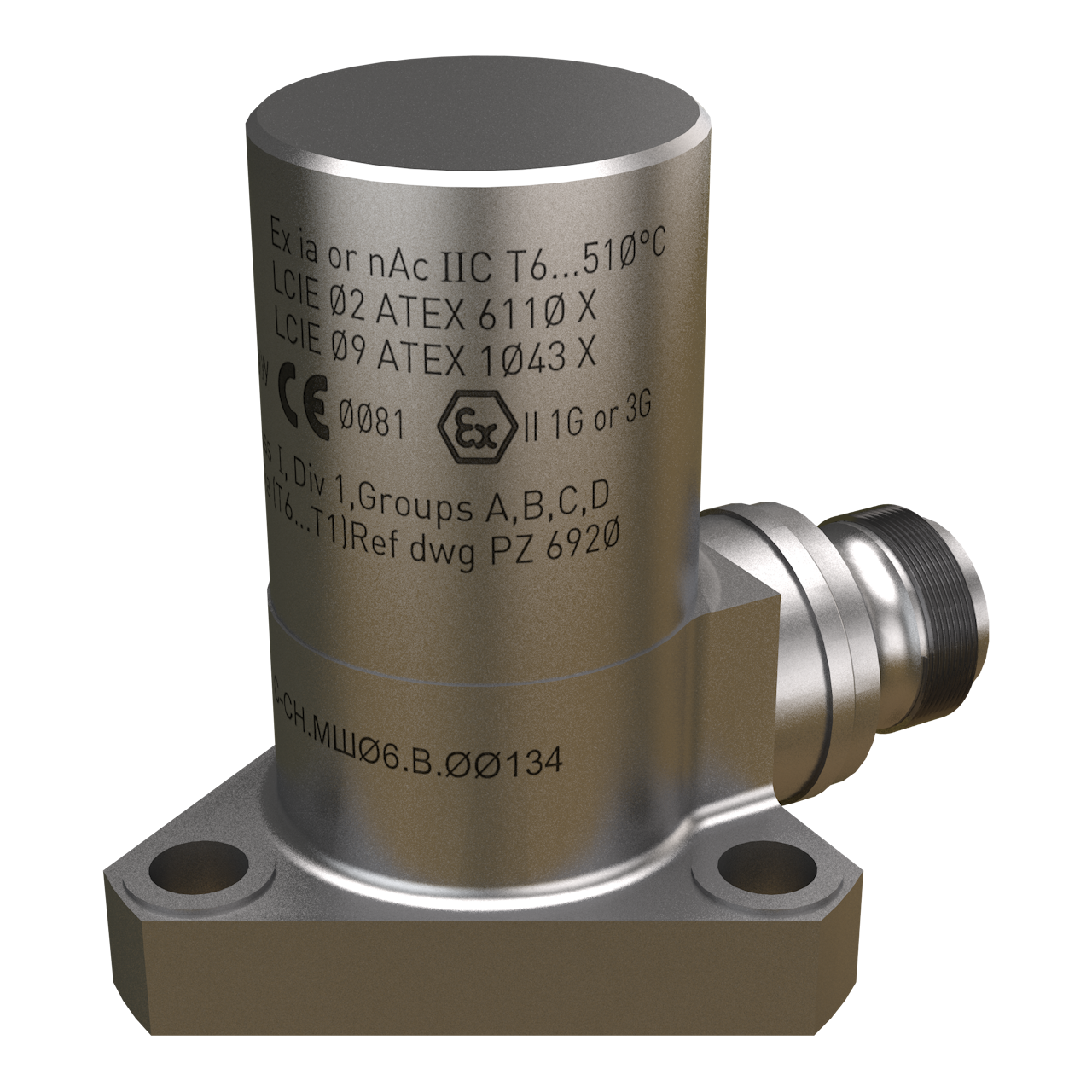

The focus of this circuit note is on the application of this solution to vibration applications, especially in the area of condition-based monitoring, but there is a large set of applications in instrumentation and industrial automation that use IEPE sensors in a similar way and that are served by similar signal chains.Ĭondition-based monitoring, in particular, uses sensor information to help predict changes in the condition of a machine. The most common IEPE sensors are usually found in applications measuring vibration, but there are many IEPE sensors that measure parameters such as temperature, strain, shock, and displacement. The reference design shown in Figure 1 shows a high resolution, wide bandwidth, high dynamic range, Integrated Electronics Piezoelectric (IEPE)-compatible interface data acquisition (DAQ) system that interfaces with IC Piezoelectric (ICP ®)/IEPE sensors. Simplified Circuit Diagram (All Connection and Decoupling Capacitors Are Not Shown) The analog filter of the system rejects frequencies at multiples of the sampling frequency, eliminating aliasing concerns. The ADC has fully programmable digital filters with adjustable bandwidth and data rate that can be tailor fit to specific system requirements. The low input bias current minimizes the dc error due to the output impedance of the sensor, and the high common-mode rejection ratio (CMRR) minimizes the impact of the common-mode noise pickup from the environment, especially when the sensor is located far from the DAQ system, which keeps the dc errors to a minimum, while not making sacrifices to the ac performance of the converter. The dc and ac performance of this system have been optimized to provide exceptional performance across the entire analog input bandwidth. The system has a programmable gain block for attenuation or amplification of the input signal to optimally utilize the input range of the ADC. The wide input voltage range, high input impedance, and high input common-mode voltage allows most sensors and signal sources to be connected directly to the input, without additional signal conditioning. The DAQ system shown in Figure 1 has simplified many of these design challenges into a single, flexible DAQ platform that can be used across a wide range of ac and dc applications. Others are designed to provide superior ac performance, with low distortion and flat frequency response. Some DAQ systems are designed to minimize the overall system dc error from the sensor, with fast settling filters for control loop or multiplexed applications. Components for a DAQ solution are selected on a per application basis. A typical DAQ system is comprised of a sensor, analog filtering and signal conditioning circuitry, an analog-to-digital converter (ADC), and a digital controller. A data acquisition (DAQ) system measures real-world physical phenomenon, such as temperature, force, acceleration, or vibration, converting measurements into digital values for data processing, storage, or transmission to a remote location.
